With the rise in population, and an increase in the flow of information among countries due to globalization, consumer’s products demands are increasing day by day. It is creating many environmental issues for the human beings and environmental aspects. The demand for eco-friendly and bio-degradable packaging boxes and shopping bags are increasing in markets due to rising pressures on the business sector to produce sustainable products.
What is kraft paper and what makes it so popular?
Kraft paper bags are basically used for packaging solutions. Businesses are always on the lookout for a refined packaging to make their products look good and for a better brand image. Kraft paper bags are known to be a flexible packaging option as well as a durable one for brand’s products. You must have noticed that spices, pastries, bread, dried fruits, and nuts are packed in paper bags. Served for multi purposes, paper bags can help various types of business industries in different ways.
The fact that people are becoming more and more eco-conscious; Kraft paper bags are finding their ways in the market and are gaining popularity among consumers.
Manufacturing of Kraft paper:
Kraft paper is a paper produced from kraft process. Through the kraft process, kraft pulp is made. Pulp produced by the kraft process is stronger than that made by other pulping processes. Kraft pulp is darker than other wood pulps, but it can be bleached to make very white pulp. Fully bleached kraft pulp is used to make high-quality paper where strength, whiteness, and resistance to yellowing are important. kraft paper is produced on paper machines with moderate machine speeds. The raw material is normally softwood pulp from the Kraft process. Wood for sack paper is made from softwood by the kraft process. The long fibers provide the paper its strength and wet strength chemicals are added to even further improve the strength. Both white and brown grades are made. Sack paper is then produced on a paper machine from the wood pulp. The paper is micro creped to give porosity and elasticity. Micro creping is done by drying with loose draws allowing it to shrink.
This causes the paper to lengthen 4% in the machine direction and 10% in the cross direction without breaking. Machine direction elongation can be further improved by pressing between very elastic cylinders causing more micro creping. The paper may be coated with polyethylene to ensure an effective barrier against moisture, grease, and bacteria. A paper sack can be made of several layers of sack paper depending on the toughness needed. He Kraft process can use a wider range of fiber sources than most other pulping processes.
The Kraft pulping process:
We make kraft pulp by mixing wood fibers with a solution of caustic soda and sodium sulfide and cooking them inside a digester. This separates the fibers from the lignin, which is a natural glue-like substance that binds them together. Our production facilities are designed to recover and reuse much of the water, chemicals, and steam used in the process. This process includes the following steps which are given below.
Wood chips:
The main ingredient of kraft pulp is wood fiber in the form of chips. A typical wood chip measures 40 x 25 x 10 mm and is a leftover from lumber manufacturing. They are stored in a silo after delivery to the pulp mill. To produce pulp, the wood chips must be broken down into their individual cellulose fibers.
Digester and Blow Tank
A digester is a large tank, between three and six meters in diameter. Inside it, a combination of chemicals, heat, and pressure dissolve the lignin and begin the process of converting chips to the pulp. From the digester, the fiber goes into a blow tank, where a rapid change in pressure causes the wood to separate into individual fibers.
Screening and Washing
Screens remove any fiber bundles that have failed to separate, and they are reprocessed. The pulp is also washed thoroughly to remove chemicals and dissolved lignin. The pulp, now a brown-colored combination of individual wood fibers and water, is then stored to wait to bleach.
Bleaching:
Bleaching is five-step processes of soaking and washing within a vertical tower, using a hydrogen peroxide, chlorine dioxide, oxygen, and caustic soda. This both dissolves any remaining lignin and turns the brown pulp fibers white. We use an elemental chlorine-free bleaching process. Then it’s on to another storage tank to await pressing and drying.
Pressing and dying:
The pulp is now slurry which is converted into sheets by being passed through a sheet former, where water is drained due to gravity and suction. Then, sheets pass through the press before sections which squeeze out more water before heading for the dryer. Here, steam heated engine jets reduce water content less than 10%.
Pulp bales:
Once out of the dryer, sheets are immediately cooled to keep their color consistent. They are then cut into smaller sheets and baled. A hydraulic press compacts the bales before they are wrapped for shipment to customers. Bales typically measure 81 x 85 x 38 cm and weigh 250 kg.
What should be the qualities of quality kraft paper?
In markets, the demand for those products is high which have quality and strength. Similarly, kraft paper has to be used in various packaging boxes and shopping bags. Therefore, kraft paper should have the maximum elastic limit which means that it should have the capability to withstand the maximum load in it.
In addition to it, Kraft paper should be durable and can protect the boxes for long. Those companies acquire maximum profit from its business if they will use packaging boxes which are durable and reliable.
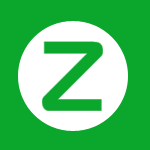